Introduction
Laser scanning is the process of capturing three-dimensional spatial data in the form of a point cloud using lasers.
Laser scanning is widely used because of its capability to properly measure and collect data from objects, surfaces, structures, and landscapes. Laser scanners acquire data in the form of point clouds, which are composed of millions of three-dimensional coordinates (X, Y, Z coordinates).
Laser scanning eliminates data collection mistakes and need to re-visit the site in case of any missing details. It is mostly used to create 3D scans (or models) of building elevations, floor layouts, tunnel profiles, and highway/rail bridges, as well as to map topography.
Laser scanning is an effective method, when there are requirements of precise 3D measurements and accurate models are to be developed. There are various 2D and 3D applications that can make use of laser scanner data once it has been cleaned up.
Leica, Trimble, Faro, Riegl, Topcon etc. are some of the market leaders in the manufacture of Laser Scanners.
History of Laser Scanning
In the 1960s, the first 3D scanning technology was developed. The earliest scanners accomplished this task by the use of lights, cameras, and projectors. Due to the limitation of the scanning equipment, it requires a considerable amount of time and effort to generate accurate scan of objects.
After 1985, they were superseded with LiDAR systems that could capture a surface using white light, lasers, and shadowing. Back then various technologies were used to develop 3d scanning devices, each with its own limit, benefits, and cost. For example, the optical scanning technologies has the limitation to scan bright, reflecting or transparent objects.
The 3d laser scanning technology has been evolving since then and now we are experiencing accurate and more photo-realistic scans. Modern laser scanners can gather detailed point clouds, and these datasets may be used to construct digital 3D representations of the scanned area using point cloud processing software.
Types of Laser Scanners
The Laser Scanners can be broadly divided into three (3) categories based on the technology used. All scanners work on the same principle of sending out laser pulses, but they differentiate in how they capture the return signals.
- Time of Flight Laser Scanners
- Phase Based Laser Scanners
- Laser Triangulation Scanners
Time of Flight Laser Scanner
The time-of-flight laser scanner works based on the same principle of a Laser Range Finder. It basically measures the distance from an object by capturing the time taken for the signal to bounce back from the target object.
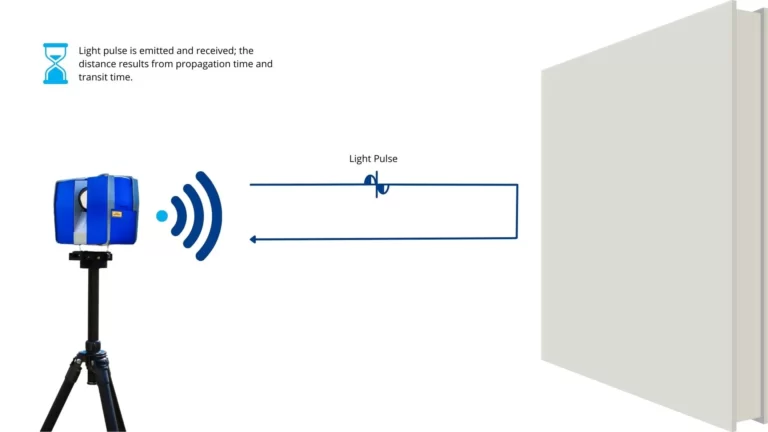
The time-of-flight scanner operates based on the below formula:
Distance = (Speed of Light x Time-of-flight)/2
Based on the time taken for the signal to return, the scanner function to determines the distance to the target object and the horizontal and vertical angle for every position it is at, in a grid fashion, 360° horizontal plane and approximately 330° vertical plane.
For the area scanned, the distance measured is used to calculate the 3d coordinates (x, y, z) for each point. With a Single scan, a laser scanner captures a million points with the respective 3d coordinates. The point cloud generated from the laser scanner are processed to generate the digital representation of the scanned surface.
The time-of-flight scanner requires higher scanning time when compared to a phase shift scanner, but these scanners can be used to cover a larger area (up to 2km). In most cases, a time-of-flight scanner will only be utilized if a phase shift laser scanner is not feasible due to the distance involved. For example, the time-of-flight laser scanners are mainly used for the scanning of mines, tunnels and caves.
Below are some of the best-know Time-of-flight method-based Laser Scanners available in the market:
- Leica RTC360 (Range: 0.5m to 130m)
- Optech Polaris Laser Scanner (Range: 1.5m to 250m / 750m / 2,000m)
- Riegl VZ-2000i (Range: 1m to 2,500m)
- Trimble X7 3D Scanner (Range: 0.6m to 80m)
- Topcon GLS-1500 (Range: up to 330m)
Phase based Laser Scanners
The phase-based laser scanner works on the following principle of determining an object’s distance by the difference in phase shift between the incoming and departing signals (in other words, computing a “shift” or “displacement”). These scanners use a constant beam of laser beams from the scanner and measure the phase shift to calculate the distance and everything else works in the same principle as that of a time-of-flight scanner.
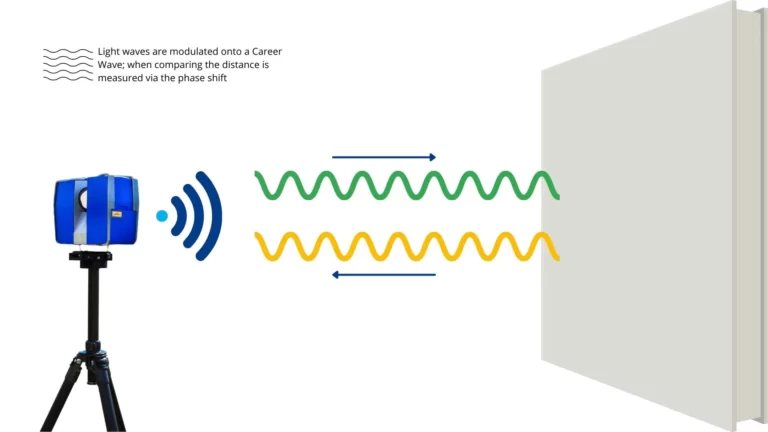
The Phase based laser scanner operates based on the below formula:
Time-of-Flight (TOF) = Phase Shift / (2π x Modulation Frequency)
In comparison to a time of flight, this scanner is far more precise and has a scanning range of 300 meters. This scanner is more adaptable than the time-of-flight scanner and is utilized in a variety of project environment including heritage, archaeology, architecture, and civil engineering projects.
Below are some of the best-know Phase Based Laser Scanners available in the market:
- ARTEC Ray (Range: 1m to 110m)
- FARO Focus M 70 (Range: 0.6m to 70m)
- Leica RTC360 (Range: 0.5m to 130m)
- Leica BLK360 (Range: 0.6m to 60m)
- Zoller + Fröhlich Imager 5016 (Range: up to 360m)
Laser Triangulation Scanners
Triangulation Laser Scanners are used to scan object which requires micron level detail. These are generally used for short scans ranging from 0.5 – 2m. A triangulation laser scanner works based on trigonometric calculation and it comprises of three (3) main elements a laser scanner, camera and the object to be scanned placed on a rotating plate to obtain the scan of different faces.
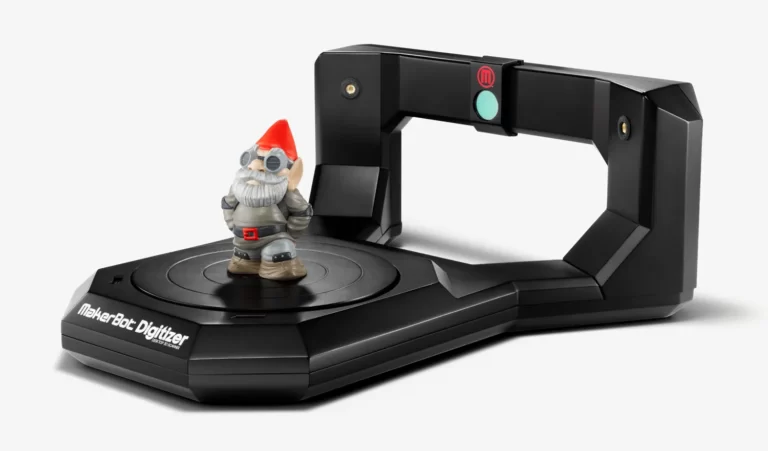
These scanners come at low price and is popular for its precision level (of the order of 0.01 mm) and acquisition speed (less than 10 minutes on average for an object).
The noted disadvantage of these scanners is its inability to digitize reflective or transparent surfaces and the short range of scanner limits the use in a number of different applications.
- Matter Form
- MakerBot Digitizer
- Faro’s Focus3D
- BQ Ciclop
Converting Laser Scan to Revit & 3D Models
The complete point cloud scan can be imported into various 3d modeling software like Autodesk Revit to act as a reference for exiting structures in an on-going project or can be used for renovation or refurbishment projects. Laser scanning can be an excellent choice to create precise drawings and 3d models for existing conditions.
Check out our Scan to BIM Services page or drop an email to [email protected] to know more about how BIMEX Engineers can support you in point cloud to BIM Modeling.
Conclusion
As more construction projects use 3D models and BIM, working on point cloud becomes extremely beneficial. There is no doubt that these comprehensive 3D models add to the efficiency and success of a project. By developing these models using solid data on present situations, they become exponentially more effective.
Laser scanning is currently the best way to obtain precise data and is projected to become the gold standard in the future.
The process ensures cost savings and efficiency due to its capability for accurate data collection within a short span of time and the lower labour requirements for performing the same.